The melt layer is sort of thin; for example, when cladding an aluminum alloy it is about 0.5–4μm (Kreye 1985, 1997 ). The dilution of the molten zones results in plane or corrugated interfaces. During mechanical decladding, the gasoline assemblies are chopped and the gas core is leached with nitric acid, abandoning the undissolved cladding materials for disposal as a strong waste.
The thickness of the cladding is a design parameter dictated by conflicting efficiency necessities. The effect of loss of steel by inner or outer corrosion is much less essential for thick cladding than for skinny-walled tubing.
The compromise between these competing demands has produced wall thicknesses of ∼0.9mm in BWRs and ∼0.7mm in PWRs. Laser cladding normally entails overlaying a comparatively inexpensive substrate materials with a more expensive alloy that may improve the resistance of the part to put on or corrosion.
Zircaloys also endure from bad creep rates. In distinction to floor-layer welding, explosive welding causes no change in microstructure, and corrosion resistance of the layers isn't affected (Pocalco 1987 ).
In our cladding options we consider the styling and colors, choice of supplies, lighting design and total setting of the constructing as key CI components, so that every thing matches your individual requirements. Although the thermal properties of façade coverings was of primary importance, right now corporate identification (CI) aspects are crucial to the design of the panels. ACM (aluminium composite), glass, natural stone and sheet metal are simply a few of the materials that can be used in the wide variety of plate-holders and sections. , where T is the absolute temperature and β is the burnup.
is produced and the risk of a large secondary hydriding failure is elevated. In response to this unforeseen consequence, several fixes were launched.
Increased put on and oxidation resistance of titanium aluminide alloys by laser cladding Euro Superalloys. Increased put on and oxidation resistance of titanium aluminide alloys by laser cladding. A structured separating layer, consisting of a three-layer vapour-permeable roof underlay membrane with self-adhesive butyl strips, bonded to monofilaments arranged in a random community, for use as a spacer layer between the roof construction and the steel cladding. Those areas subjected to excessive warmth - from the exhaust manifold or catalytic converter for instance - would be insulated by a refractory materials and steel cladding. Wire-based laser deposition welding is a cloth-efficient 3D printing course of for the production of metallic parts.
This method is adopted for zircaloy-clad fuels from power reactors and chrome steel-clad fast reactor fuels. Like the cladding , underneath the effect of neutron flux the hexagonal wrapper tube undergoes change. Geometrical adjustments, induced by swelling and irradiation creep (under the effect of dynamic sodium pressure), concern length, across-flat dimension, and, for subassemblies positioned within the periphery of the core, bowing (differential swelling induced by differential flux and temperature between opposite faces of the wrapper tube).
Today, Zircaloy-2 and Zircaloy-4 are broadly used. Phase transformation of Zirconia is, nevertheless, of nice concern.

Applications for Surface Treatment
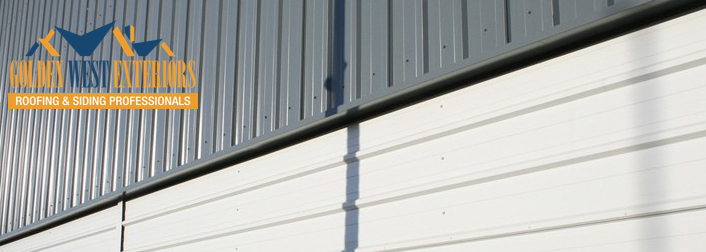
Once the pellet/clad hole is closed, any change in pellet dimensions causes stress in the cladding and the synergy between the stress and the corroding medium induces the SCC process. In order to prevent or minimize pellet/clad interactions, each mechanical and chemical, a coating of graphite powder is utilized on the inner surface of cladding tubes.
Increased put on and oxidation resistance of titanium aluminide alloys by laser cladding Euro Superalloys. Increased put on and oxidation resistance of titanium aluminide alloys by laser cladding. A structured separating layer, consisting of a 3-layer vapour-permeable roof underlay membrane with self-adhesive butyl strips, bonded to monofilaments organized in a random network, to be used as a spacer layer between the roof construction and the steel cladding. Those areas subjected to excessive heat - from the exhaust manifold or catalytic converter for instance - could be insulated by a refractory materials and steel cladding. Wire-based laser deposition welding is a fabric-environment friendly 3D printing course of for the production of metallic components.
is produced and the danger of a large secondary hydriding failure is elevated. In response to this unexpected consequence, several fixes had been introduced.
Our huge vary of products includes PVC wall panels, outside wall cladding, waterproof flooring as an alternative to laminate or LVT, water-resistant shower and loo panels and much more. These embody cladding, small metal pins coupled with a ceramic mass, half-pipes and SiC tiles, in addition to varied types of coatings, together with thermal spray coatings. Its characteristic function is the sash bar down the middle of the window and black (just like RAL 9005) metallic cladding coverings on the window and flashing which matches conventional buildings. The Independent Expert Advisory Panel additionally advised the department to establish a analysis project to test and improve the evidence out there on the behaviour of a spread of non-ACM materials utilized in cladding techniques when subjected to fireside.
Joining happens continuously by local plastic deformation of the contact space (Ruge 1993 ) (see Fig. 1 ). Figure 6 . Schematic diagram exhibiting the mechanism of the oxidation course of and the oxide film structure on zircaloy. Figure 5 .
Cladding permits the majority of the half to be made with inexpensive material, while offering the surface with fascinating properties related to the dearer cladding material. Laser cladding has resulted in surfaces with excellent end, good homogeneity, and very low porosity. Common materials used for cladding include carbides, iron-based mostly alloys, nickel base alloys, and cobalt base alloys. Laser cladding is a course of by which a metallic coating is applied onto the floor of a part using a laser as the heat supply.
Non-aluminium composite see page materials Home Page cladding
Long-term, in-reactor, oxidation, and hydrogen decide up conduct of zircaloy-2 and Zr-2.5Â Nb strain tubes, showing parabolic and then accelerated linear oxidation and hydrogen pickup kinetics in zircaloy-2. A low and uniform rate of corrosion and hydrogen decide up is seen in the in Zr-2.5Â Nb alloy. Differential swelling between cladding, wrapper tube, and spacing system (spacer wire or grids) can induce further stresses and deformations on these parts and/or generate coolant flow perturbations in the bundle. These phenomena have been studied and have significantly shown that wires or grid materials should be chosen and specified in order to reduce differential swelling.
With it, we process individual elements in addition to collection elements, inside as well as outer contours, new and used parts. Cladding in construction is material utilized over another to supply a pores and skin or layer and used to supply a degree of thermal insulation and weather resistance, and to enhance the appearance of buildings. Between the cladding and the wall there's a cavity the place rain can run down. Laser cladding with the help of power-based mostly or wire-shaped filler supplies can be used for repair work, the applying of wear and tear and corrosion safety and the production of 3D elements (additive manufacturing).
The soften layer is sort of thin; for instance, when cladding an aluminum alloy it's about 0.5–fourμm (Kreye 1985, 1997 ). The dilution of the molten zones leads to airplane or corrugated interfaces. During mechanical decladding, the gas assemblies are chopped and the fuel core is leached with nitric acid, leaving behind the undissolved cladding material for disposal as a solid waste.
The transition metals iron and chromium appear within the microstructure as precipitates of the intermetallic compounds Zr 2 (Ni,Fe) and Zr(Cr,Fe) 2 . These minor alloying elements enhance corrosion resistance to an extent dependent on the size of the precipitates. Laser cladding has been utilized to hardening of steam generator turbine blades and reached pilot production status [four ]. The blades had a machined pocket, into which powdered cobalt-based mostly steel (Stellite 6) was fed forward of the laser beam.
The effect of thermal conductivity degradation on the performance of the gas is illustrated in Fig. 1 . This reveals the results of calculations during which the ability in a rod is artificially held at a relentless degree.
The compromise between these competing demands has produced wall thicknesses of ∼zero.9mm in BWRs and ∼zero.7mm in PWRs. Laser cladding usually entails overlaying a comparatively inexpensive substrate material with a costlier alloy that can enhance the resistance of the part to wear or corrosion.

Laser my latest blog post Cladding
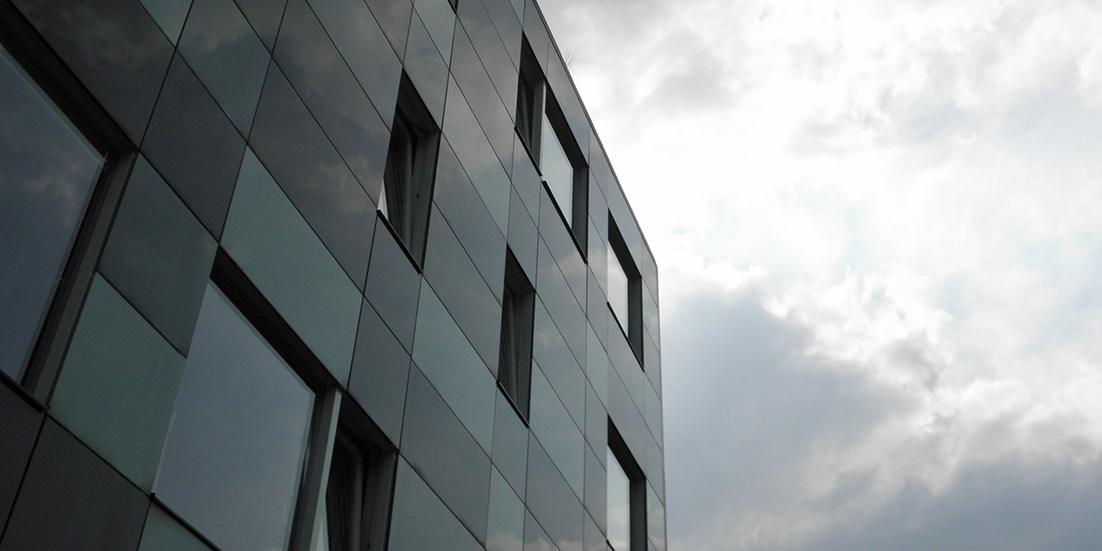
This technique is adopted for zircaloy-clad fuels from power reactors and stainless-steel-clad quick reactor fuels. Like the cladding , under the effect of neutron flux the hexagonal wrapper tube undergoes change. Geometrical modifications, induced by swelling and irradiation creep (under the impact of dynamic sodium stress), concern size, across-flat dimension, and, for subassemblies placed within the periphery of the core, bowing (differential swelling induced by differential flux and temperature between reverse faces of the wrapper tube).
These approaches have encountered issues, together with porosity of the cladding, uneven cladding thickness, dilution of the cladding alloy due to the big heat input required, and distortion of the workpiece by the high heat enter. Laser cladding has reduced these problems and produced cladding layers with good uniformity, good dimensional control, and minimal dilution of the cladding alloy. provides a survey of a cladding equipment. If the incoming strips need to be heated so as to lower the energy of materials, this must be accomplished as shut as attainable to the rolling hole and in a protecting atmosphere in order to avoid oxidation of the cleaned and roughened surfaces. We provide high-quality ornamental merchandise that improve any house and inside.
In addition to metallurgical factors, water chemistry has a strong influence on the corrosion course of in zirconium alloys. The management of water chemistry as required in several reactor systems embody appropriate additions of lithium hydroxide, boric acid, hydrogen/deuterium, oxygen, iron, and zinc. In PWRs, boric acid is added to the coolant water for reactivity management. The pH of the coolant is adjusted by addition of lithium hydroxide which renders the coolant slightly alkaline, to be able to cut back the corrosion charges of structural supplies (stainless steels and Inconels) within the primary warmth transport circuit and thereby inhibit deposition of corrosion products on the fuel cladding. Radiolysis of water produces oxidizing species which boosts oxidation rate of zirconium alloys within the radiation environment .
Cladding allows the majority of the half to be made with inexpensive material, while offering the floor with fascinating properties related to the dearer cladding material. Laser cladding has resulted in surfaces with superb end, good homogeneity, and really low porosity. Common materials used for cladding include carbides, iron-based alloys, nickel base alloys, and cobalt base alloys. Laser cladding is a course of during which a metal coating is utilized onto the floor of a component using a laser as the heat supply.
This is a main cladding failure that admits steam into the rod with the accompanying potential for a extra critical secondary failure due to hydriding. The combination of conditions (susceptible metal, tensile stress, and chemical enhancer) that produces the primary defect is termed pellet–cladding interplay (PCI). scale that grows around them during in-reactor operation. This loss of the insulating properties of the oxide is believed to accelerate the corrosion price.
laser. The clad substrates showed improved oxidation traits compared with the original alloy. Conventional methods for cladding have employed tungsten-inert gas welding, plasma spraying, and flame spraying.
Moreover, embrittlement owing to irradiation or temperature has to be mastered so as to avoid rupture in the reactor or in the course of the back-end of the cycle (handling, washing, and so forth.). Cold-worked austenitic steels (with composition closed to that of the cladding) have been used first but at the moment are frequently changed by extra swelling-resistant ferritic–martensitic steels (9Cr kind), in so far as the height wrapper temperature, decrease than that of cladding, allows avoidance of thermal creep problems.
The complete melting of the filler leads to a dense layer with optimal adhesion to the substrate. The commonest application is for the damage protection, e.g. of instruments, but additionally corrosion protection or high temperature resistance may be particularly improved. Common onerous alloys primarily based on cobalt, nickel and iron are used with and with out the addition of exhausting materials. But additionally particularly tailored materials may be utilized.
The impact of thermal conductivity degradation on the performance of the gas is illustrated in Fig. 1 . This reveals the results of calculations by which the ability in a rod is artificially held at a constant degree.
In our cladding solutions we think about the styling and colours, selection of materials, lighting design and overall setting of the constructing as key CI elements, so that every thing matches your particular person requirements. Although the thermal properties of façade coverings was of primary importance, right now corporate id (CI) elements are crucial to the design of the panels. ACM (aluminium composite), glass, natural stone and sheet steel are just a few of the supplies that can be utilized in the wide range of plate-holders and sections. , the place T is the absolute temperature and β is the burnup.
The ensuing cladding layer was well bonded, and the blades exhibited improved fatigue characteristics compared with blades formed by the conventional silver brazing course of. laser beam. The alloy was overlaid on the metal as a powder layer 2.5 mm thick. After melting and bonding by the laser, the alloy layer was 1.5 mm thick and had very little dilution from the steel. The resulting surface had glorious wear resistance.
The filler materials can either be supplied in powder type e.g. as metal powder, or with a welding wire. When laser cladding is carried out utilizing powder, the laser usually heats the workpiece with a defocussed laser beam and melts it domestically. At the identical time, an inert gasoline mixed with a fine metal powder is launched. The steel powder melts at the heated space and is fused to the surface of the workpiece.